Bovada
DISFRUTA DE UN BONO DE BIENVENIDA DE $750
Juega Ahora
Sólo para clientes nuevos. Se aplican las condiciones generales, 18+.
Best Choice
BetOnline
OBTENGA UNA BONIFICACIÓN DE DEPÓSITO IGUALADA DEL 50% HASTA $1000
Juega Ahora
Sólo para clientes nuevos. Se aplican las condiciones generales, 18+.
BetAnySports
OBTENGA UNA BONIFICACIÓN DE DEPÓSITO IGUALADA EN UN 35% HASTA $700
Juega Ahora
Sólo para clientes nuevos. Se aplican las condiciones generales, 18+.
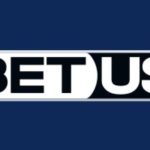
BetUS
Jugar
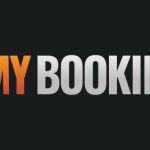
My Bookie
Jugar
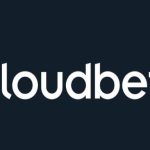
Cloudbet
Jugar
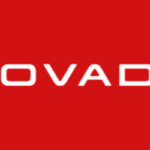
Bovada
Jugar
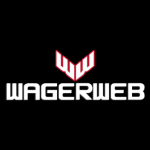
WagerWeb
Jugar
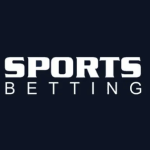
SportsBetting.ag
Jugar
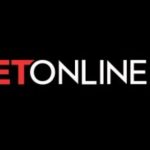
BetOnline
Jugar
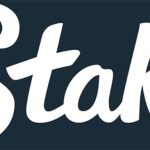
Stake.com
Jugar
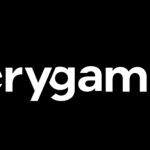
Everygame
Jugar
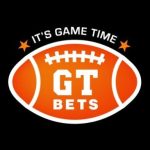
GT Bets
Jugar
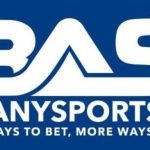
BetAnySports
Jugar
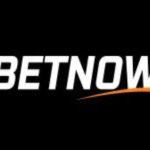
BetNow
Jugar
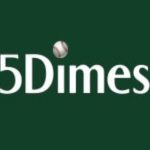
5Dimes
Jugar
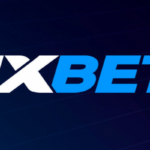
1XBet
Jugar
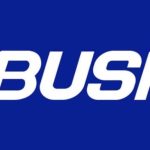
BUSR
Jugar
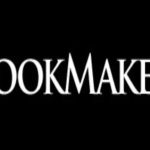
Bookmaker.eu
Jugar
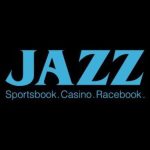
JazzSports
Jugar
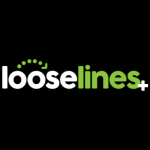
LooseLines
Jugar
Apuestas
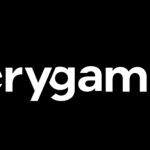
OBTENGA UN BONO DE HASTA $750
Sólo para clientes nuevos. Se aplican las condiciones generales, 18+.
Juega Ahora
Mejor
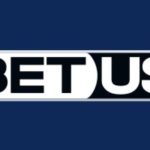
OBTENGA UNA BONIFICACIÓN DE INSCRIPCIÓN DEL 125% DE HASTA $3125
Sólo para clientes nuevos. Se aplican las condiciones generales, 18+.
Juega Ahora
Mejor
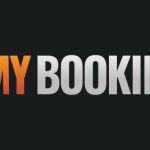
OBTENGA UNA BONIFICACIÓN DEL 100% DEL DEPÓSITO DE HASTA $1000
Sólo para clientes nuevos. Se aplican las condiciones generales, 18+.
Juega Ahora
Apuestas
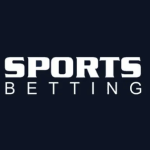
RECLAME UNA BONIFICACIÓN DEL 50% DEL DEPÓSITO DE HASTA $1000
Sólo para clientes nuevos. Se aplican las condiciones generales, 18+.
Juega Ahora